BRIEF – What is the current state of food safety in the UAE and how to use artificial intelligence and blockchain technology to create a holistic system that identifies food safety duration?
PROJECT – Contracted by the Dubai Future Foundation the project was part of their accelerator program to nurture the city’s role in progressive innovation and exponential technologies. Several multidisciplinary teams with talent from around the world were chosen to work on complex challenges across all areas of life, e.g. transport & infrastructure, education, food & water supply, administration, recreation. The aim was to prototype ideas promoting a more sustainable future for the urban ecosystem and its citizen by applying cutting-edge technologies. Dubai as the leading business hub in the Middle East is highly reliant on the import of resources and goods with most food products coming in through all possible cargo routes (land, water, air). Our project revolved around food safety and envisioned a system that would be able to track produce from the farm to the fork, ultimately get from traceability to predictability of imports. With full support by the Dubai Municipality this five week Service Design project started with intense field research to empathise with the context. Next we developed a working prototype for the Dubai Fruit & Vegetable Market (FVM) – an automated container identification as well as a container traffic management dashboard.
TEAM – Business Developer, Design Researcher, 2x Software Developer, Data Scientist
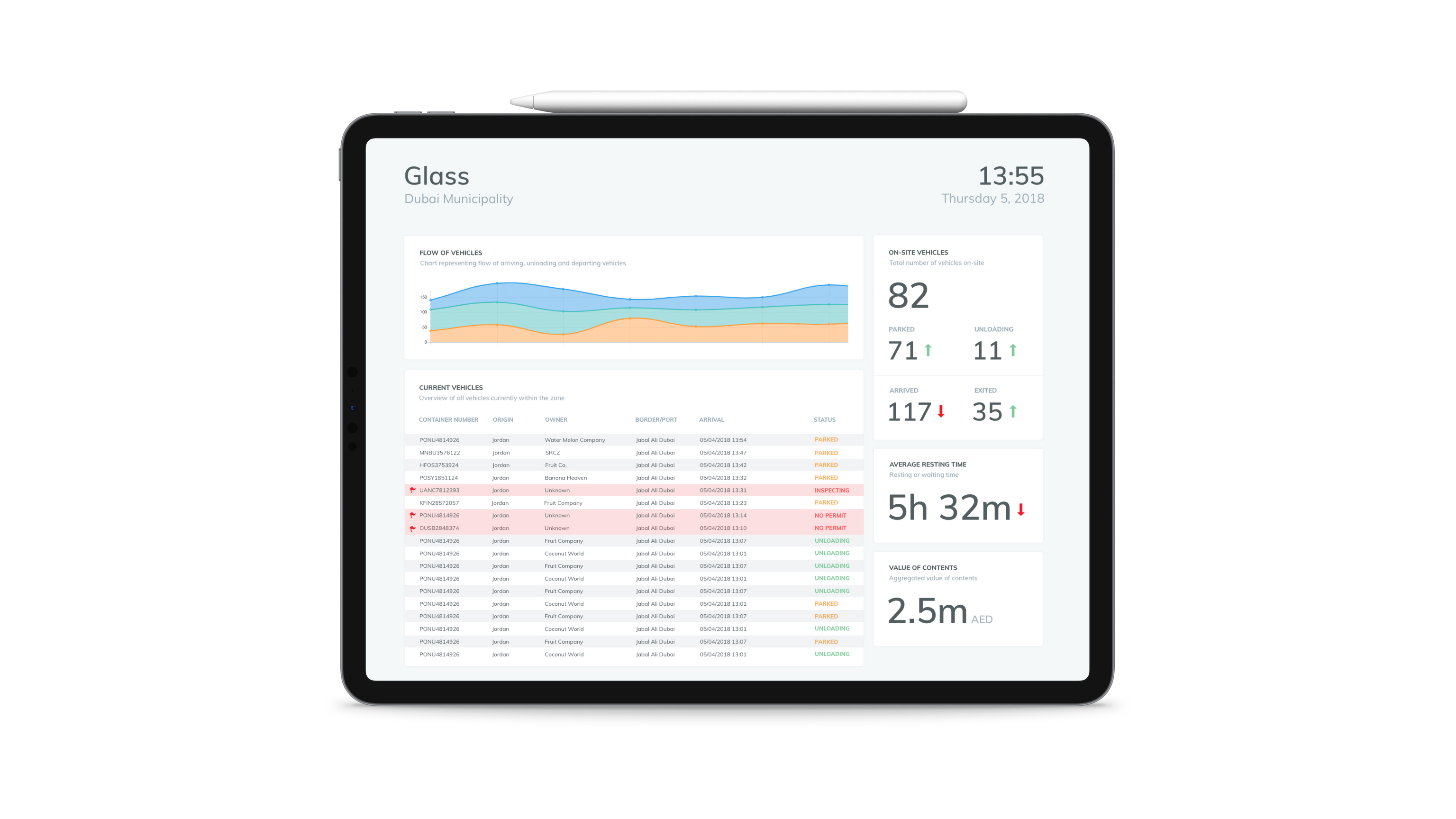
RESEARCH – In order to get an overview of the sheer dimension of Dubai’s import routes for goods from oversees, we were allowed to visit the interior and exterior of the FVM, the biggest distribution centre for foods coming from neighbouring countries as well as entry point for containers shipped to the UAE. Its infrastructure provides docks for hundreds of trucks at the same time arriving each day to create a messy market scenario in seconds out of a complete empty concrete loading structure. We inspected the large area before the trucks would arrive, observed the unloading and produce distribution, interviewed several food safety inspectors before, during, and after, and had the chance to accompany the full-process of registration. Even though though physical infrastructure was in place, incoming trucks sometimes had to wait up to 8 days to pass and unload due to an extremely manual process and understaffing of inspectors, we observed how chaotic the purchase of goods would unfold and realise how little one could monitor import’s origin, further how much waste was created due to unpredictability of demands. The local inspectors would show us the construction of new cargo docking stations, more innovative building typologies that could guarantee more thorough inspection, however manual labour dealing with a multitude of products coming in various types of container requires man power yet to be hired. Our part was to think of ways to automate certain touch points of the cargo services, thus we decided to start where we could control at least some parameters of the import process – the clearly defined entry gates at the market.
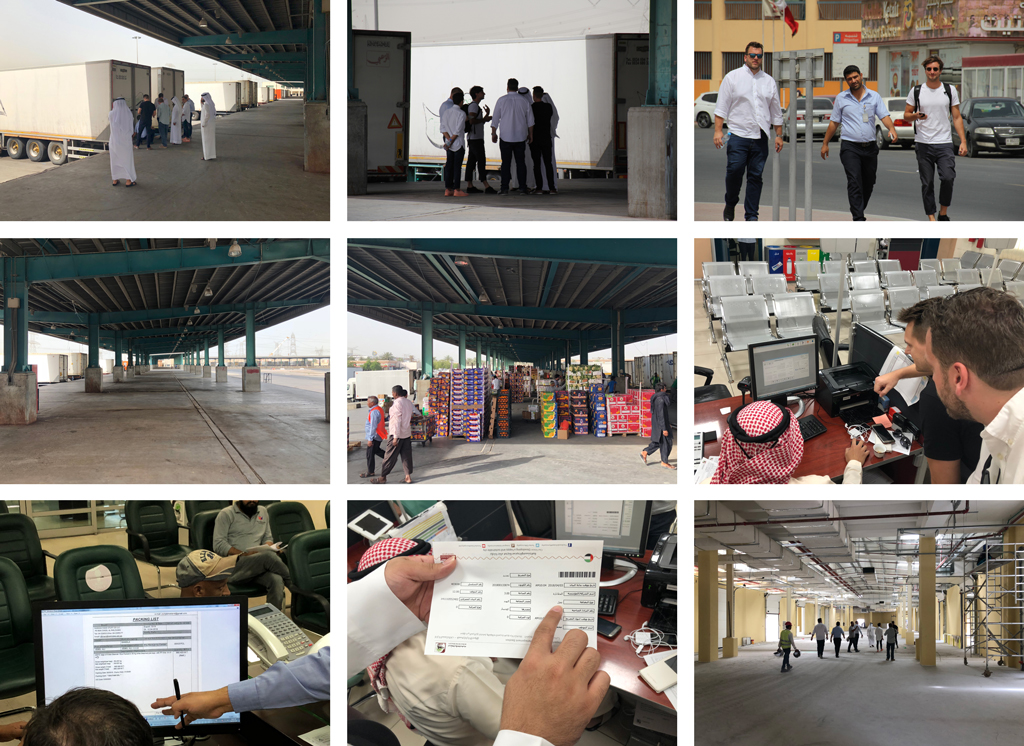
MAPPING – After walking around the area for three days exploring within the team, with and without inspectors as well as alone we could gather our intake and initially mapped out the entire market with its gates, exits, parking lots, unloading docks, entry areas for buyers and the open market area where individual reseller could start selling to the free market. The mapping informed another round of research in the field to then focus closer for challenges that might become more obvious.
CHALLENGES – Manual hand-over registration by individual buyers (incl. hotel chains, restaurants, etc.) right after unloading of the trucks immediately broke the chain, further seemingly open entry- and exit gates for buyers were identified, which clearly defined a hierarchy of control with regard to which side of the docking ramp we’d face less friction and chaos.
SERVICE DESIGN – At this point we found more important to talk to people, gathering as many insights as possible that could inform the prototype, then spending time to draw a complex service blueprint. Nevertheless, we sketched very low-fi overviews of the service and its touch points to be able to communicate to every stakeholder in simple manners the space in which we could innovate. In an ideal scenario we could track the unloading of the trucks as well as manage to follow the product hand-over and exit of buyers. First things first, we looked at the truck registration at the gates.
CONTAINER IDENTIFICATION – Inspecting the trucks fortunately disclosed clear areas of identification such as the license plate, the owner prefix (BIC code) on the container, and the manifest the truck driver carries – a written sheet of paper, tracking container contents, origins, truck routes, stops and passings. Automate part of this would be a start to digitise such important document.
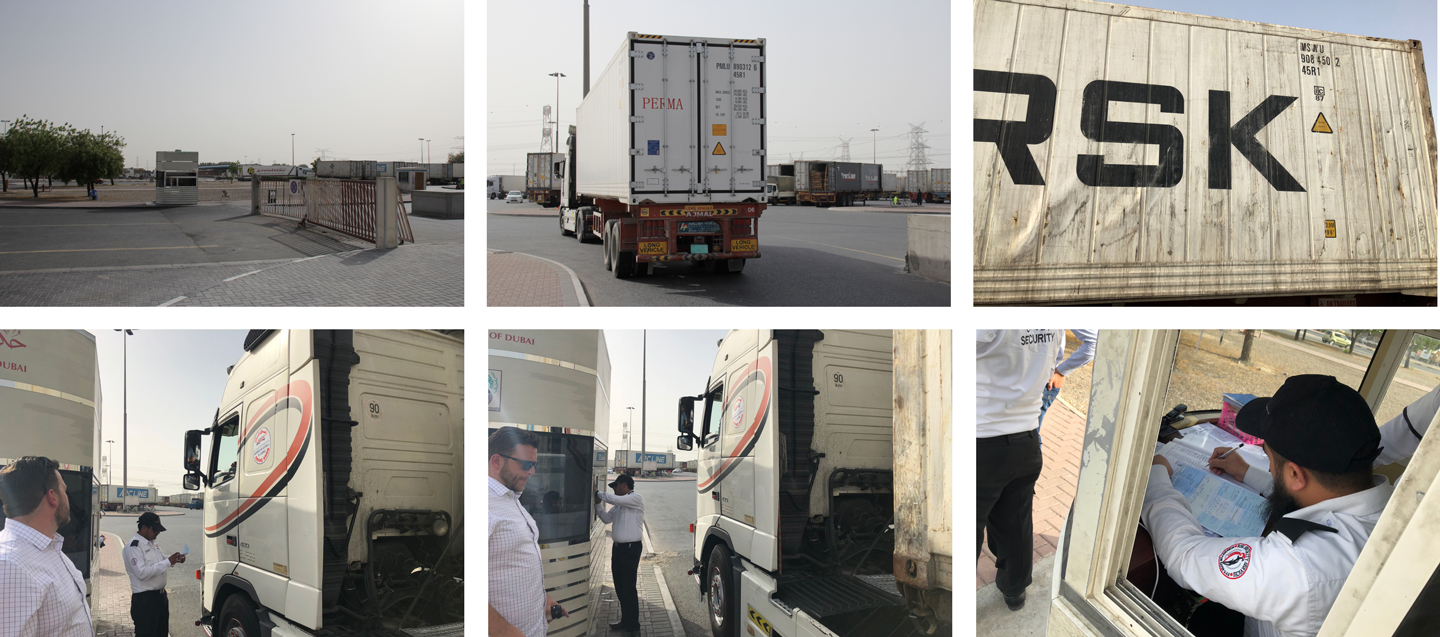
PROTOTYPE I – Phase I was meant to create an initial overview about the happenings in the FVM. The plan was to install a minimum of three cameras with hardware setup and uplink so we could track containers from entry through parking to unloading bays and exiting the FVM. In a next step a digital dashboard would process and consolidate all the data. The value of such an early iteration was clear: a first step towards tracking and monitoring, a much better ability to manage container traffic flow inside the FVM, single and aggregated statistics over time and eventually with mobile versions of the dashboard staff could be notified and alerted in real-time.
PROTOTYPE I – To prevent false / unnecessary data polluting our data set, we used a neural network as gatekeeper, a machine learning algorithm able to recognise early what kind of object arrives at the entry gate of the FVM before trying to identify and read various data points off the truck.
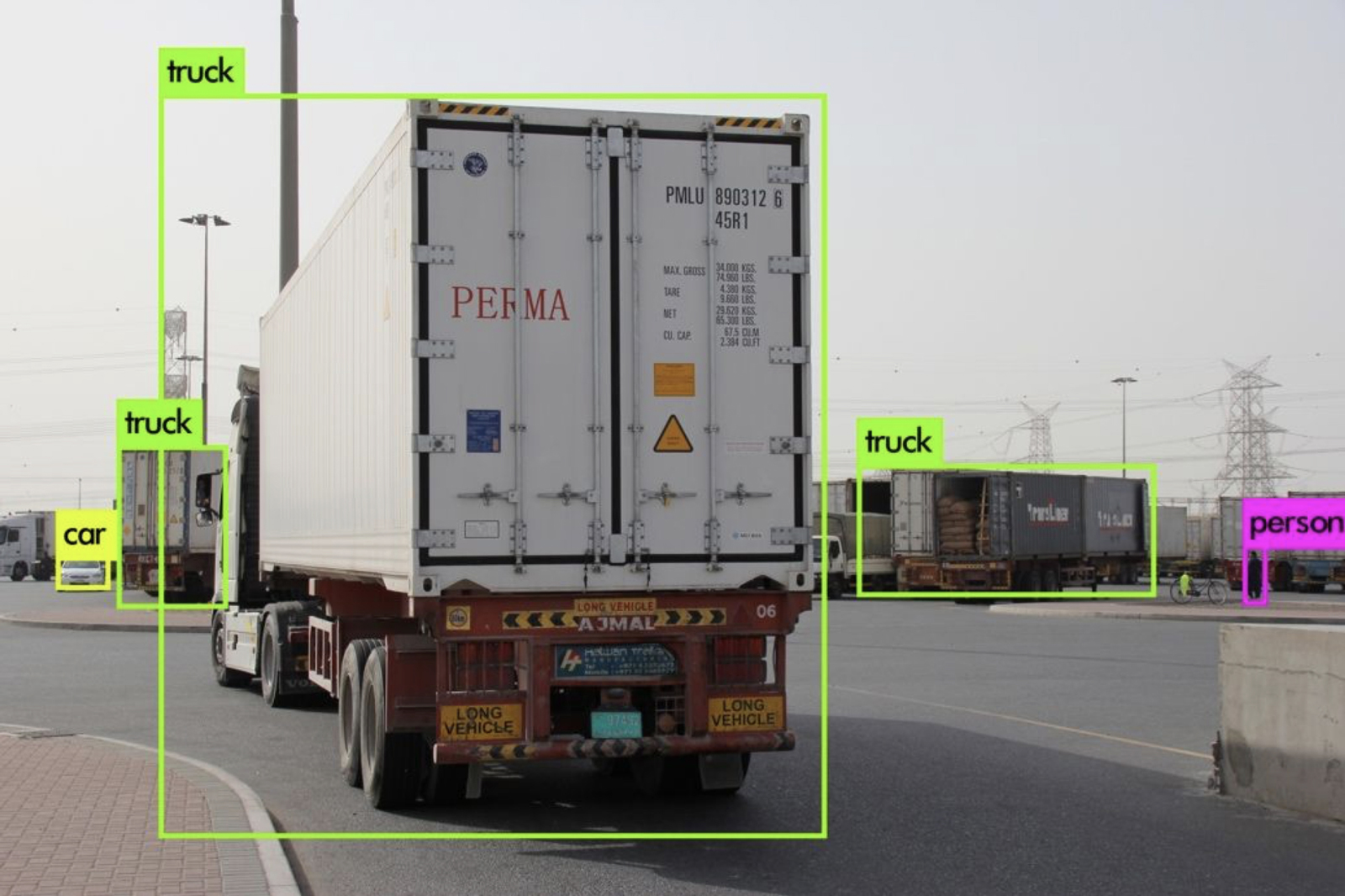
PROTOTYPE II – “Glass” became not just a dashboard that tracked container movements, but also a vision on how to integrate with manifest systems, permit systems and destruction protocols in the UAE. The dashboard was enriched with accurate data on containers consignee, goods description, value, origin, weight, PoE and could provide an overview of containers entering Dubai bound for FVM. In that way inspectors know upfront high-priority containers coming to FVM, they could identify any containers not going through FVM, see how long a container has been on the road before arriving at FVM, connect container in FVM with its manifest and permit details, a provide aggregated statistics on goods being sold, re-distributed, re-exported or sent to destruction at FVM and ultimately build a foundation for predicting estimated time of arrival for individual containers.
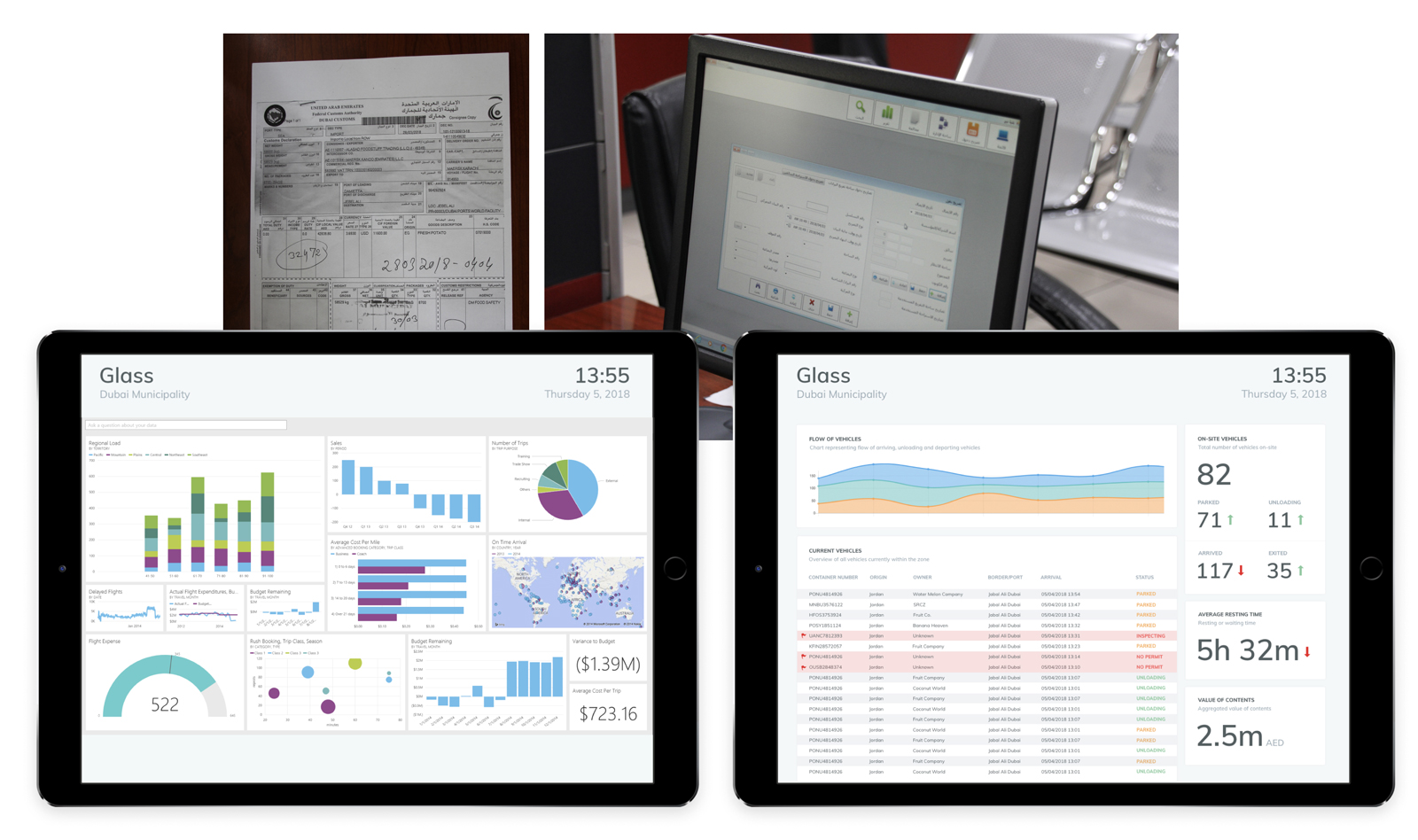
PROTOTYPE III – “Trade” became the mobile application for reporting all container trade on the unloading bay. It is connected to systems that can monitor active trades and alert simply through SMS. It provides individual and aggregated data on container trade from the unloading bay, it has the ability to send out bulk SMS warnings to all buyers of goods from one or more containers, and it could gets a unique identifier for buyers. You’d login, enter a container number, the container content will automatically appear. During trades you’d tick of the types of products sold, enter buyer ID (e.g. telephone number), and click trade to finalise the process. For us it was important to design the UI as simple as possible with only a few steps of interaction due to the messy and often fast pace situation having people from very different cultures and places interacting with each other.